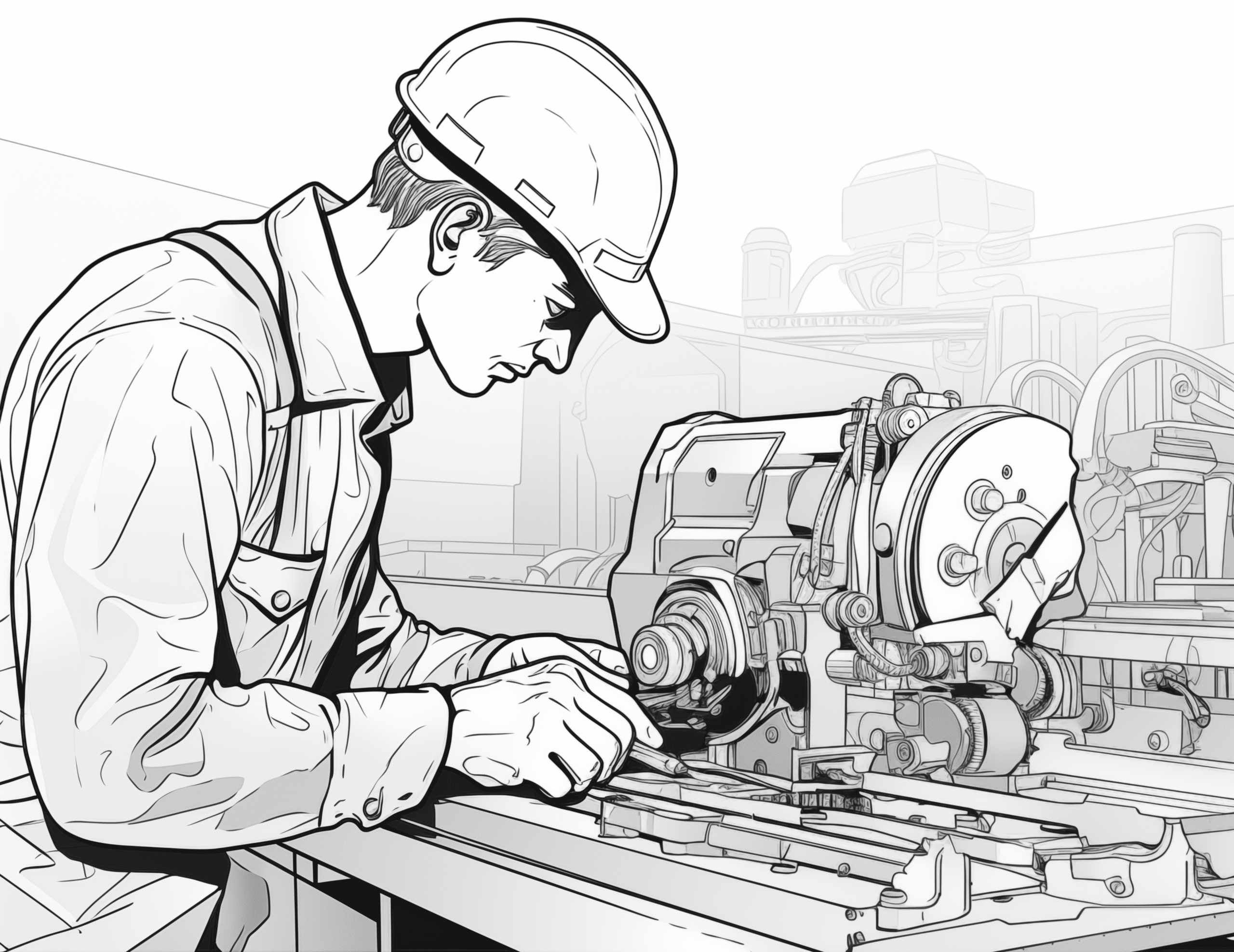
The Growing Demand and Supply for Aluminum Die Casting and Processing in Modern Industries
Aluminum die casting and processing have witnessed a remarkable surge in demand and supply in recent years, driven by the growing need for lightweight, durable, and precision-engineered components across various industries. This manufacturing process has become an indispensable cornerstone of modern industries, offering exceptional benefits that cater to the evolving demands of consumers and businesses alike.
The Rising Demand for Aluminum Die Casting
1. Automotive Advancements: The automotive industry has been a key driver of the increasing demand for aluminum die-cast components. With the global push for fuel efficiency and reduced emissions, automakers are turning to lightweight materials like aluminum to replace traditional steel parts. Engine blocks, transmission components, and chassis parts are among the many automotive applications where aluminum die casting excels, contributing to improved performance and fuel economy.
2. Aerospace Applications: The aerospace sector’s demand for aluminum die casting has grown substantially due to the material’s combination of high strength and low weight. Aircraft manufacturers rely on die-cast components for critical parts such as wing structures, engine mounts, and landing gear components. The use of aluminum not only reduces aircraft weight but also enhances overall performance and safety.
3. Electronics and Electrical Industries: The electronic gadgets we use daily, from smartphones to laptops, benefit from aluminum die casting. The process enables the creation of intricate and compact components that provide efficient heat dissipation, essential for high-performance electronic devices. Additionally, aluminum’s excellent electrical conductivity makes it an ideal choice for producing connectors and housings.
4. Consumer Goods Sector: The consumer goods industry has seen a surge in demand for aluminum die-cast products, driven by consumers’ preference for lightweight and aesthetically appealing products. Household appliances, power tools, and various handheld devices often incorporate aluminum components to offer enhanced functionality and portability.
5. Industrial Equipment and Machinery: Industries such as manufacturing, construction, and mining heavily rely on industrial machinery and equipment that leverage aluminum die casting. The material’s robustness and corrosion resistance make it suitable for producing pump housings, compressors, and other components that endure harsh operating conditions.
Supply to Meet Growing Demands
To keep up with the burgeoning demand for aluminum die casting, the supply chain has adapted and evolved to ensure a steady flow of high-quality components. Several factors contribute to the increasing supply:
1. Advancements in Casting Technology: Manufacturers are continually investing in cutting-edge casting technology to improve efficiency and precision. Computerized Numerical Control (CNC) machining, advanced simulation software, and robotics have streamlined the die-casting process, reducing production time and minimizing errors.
2. Material Innovation: Innovations in aluminum alloys have expanded the range of applications for die-cast components. By tailoring the alloy composition, manufacturers can achieve specific characteristics such as higher strength, better corrosion resistance, and improved thermal conductivity, further widening the market for aluminum die casting.
3. Capacity Expansion: As demand grows, manufacturers are expanding their production capacities to meet the needs of various industries. New facilities and production lines are established to ensure a steady supply of die-cast components.
4. Global Market Presence: The international market for aluminum die casting has expanded significantly, with manufacturers operating on a global scale. This presence allows businesses to tap into diverse markets and efficiently cater to regional demands.
Challenges and Future Outlook
While the demand and supply for aluminum die casting have experienced remarkable growth, challenges remain to be addressed:
1. Sustainable Practices: With increasing environmental concerns, manufacturers are under pressure to adopt more sustainable practices. Recycling and reducing waste in the die-casting process are becoming crucial aspects of responsible manufacturing.
2. Cost Competitiveness: As demand increases, maintaining cost competitiveness becomes essential. Manufacturers must strike a balance between producing high-quality components and optimizing production costs to remain competitive in the market.
3. Skills and Expertise: The die-casting industry relies on skilled technicians and engineers to operate sophisticated machinery and ensure quality control. Addressing the shortage of skilled professionals in the field will be vital for sustained growth.
Despite these challenges, the future of aluminum die casting and processing still appears to be promising. As industries continue to prioritize efficiency, lightweight design, and sustainable practices, the demand for aluminum die-cast components is likely to remain strong. The industry’s ability to adapt to technological advancements and meet the evolving needs of diverse sectors will determine its success in shaping the modern industrial landscape. With ongoing innovations and a focus on sustainable manufacturing, aluminum die casting at ABF LT will continue to play a pivotal role in driving progress and meeting the demands of 21st-century industries.